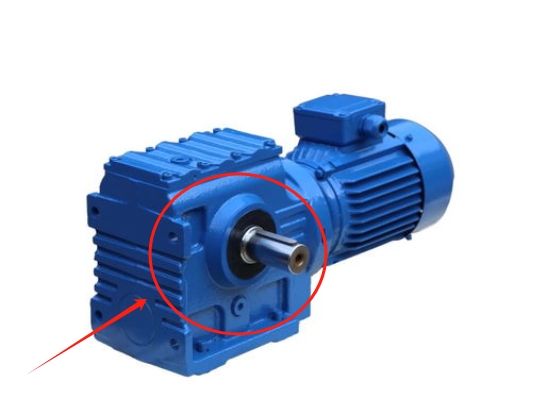
La elección del reductor de engranajes adecuado para una aplicación específica es un proceso crítico que requiere una cuidadosa consideración de varios factores para garantizar un rendimiento y una vida útil óptimos. El proceso de selección incluye varios pasos y criterios de referencia para guiar a los ingenieros a tomar decisiones informadas. Este artículo describe el proceso de selección y los criterios para el reductor de engranajes.
El primer paso para seleccionar un reductor de engranajes es clarificar los requisitos de aplicación. Esto incluye conocer el propósito del sistema mecánico, las condiciones de funcionamiento y las velocidades de salida y par requeridos. Tenga en cuenta factores como el medio ambiente (por ejemplo, temperatura, humedad y exposición potencial a sustancias corrosivas), la frecuencia de funcionamiento (intermitente o continuo) y cualquier estándar específico de la industria que se debe cumplir.
Determinar los parámetros de entrada y salida A continuación, se recopilan datos sobre la potencia de entrada y la velocidad del motor o motor conectado, así como la velocidad de salida y el par requeridos para el dispositivo impulsado. Esta información es esencial para calcular la relación de transmisión necesaria y para seleccionar el reductor de la capacidad adecuada.
La relación de transmisión calculada es la relación entre la entrada y la velocidad de salida del reductor de engranajes. Se puede calcular utilizando la siguiente fórmula: relación de transmisión = velocidad de entrada / velocidad de salida. Esta relación le ayudará a determinar el tipo de engranaje y la configuración necesaria para lograr la desaceleración deseada.
Evaluar los requisitos de par es un parámetro clave en la selección del reductor de engranajes. El par de salida del reductor debe ser mayor o igual al par de carga para garantizar el funcionamiento eficiente del sistema. Utilice la fórmula: salida de par = entrada de par / relación de transmisión. Al determinar el par requerido, tenga en cuenta los factores de seguridad y las posibles fluctuaciones de la carga.
Hay varios tipos de reductores de engranajes, como reductores de engranajes helicoidales, reductores de tornillo helicoidal, reductores de engranajes planetarios y reductores de engranajes cónicos, cada uno de los cuales tiene sus ventajas y limitaciones. Seleccione el tipo en función de factores como la velocidad y el par requeridos, las limitaciones de espacio, los requisitos ambientales y de mantenimiento.
Considere la eficiencia y el uso de la eficiencia del factor se refiere al porcentaje de potencia de entrada convertida en potencia de salida útil. Los reductores más eficientes pueden funcionar a temperaturas más bajas y tener una vida útil más larga. El coeficiente de uso es la tolerancia a las condiciones más duras en comparación con la capacidad nominal del reductor de presión. Al elegir un reductor de engranajes, se deben considerar tanto la eficiencia como el factor de uso para garantizar que pueda satisfacer las necesidades de la aplicación.
La configuración de instalación del reductor de engranajes para revisar la instalación y la opción de acoplamiento debe ser compatible con la maquinaria existente. Revise las opciones de montaje disponibles y el tipo de acoplamiento para garantizar una conexión segura y eficiente entre el reductor y el motor o el equipo de accionamiento.
Consulte los datos del fabricante y los fabricantes de estándares para proporcionar datos detallados sobre sus reductores de engranajes, incluidas las dimensiones, la capacidad de carga, la velocidad de funcionamiento y las clases de eficiencia. Normas como ISO, AGMA (Asociación Americana de Fabricantes de Engranajes) y DIN (Diploma Alemán de la Industria) proporcionan directrices para el diseño, las pruebas y el rendimiento de los reductores de engranajes. Consulte estos recursos para asegurarse de que el reductor seleccionado cumple o excede las especificaciones necesarias.
Realizar el análisis de costos del ciclo de vida no solo tiene en cuenta el costo inicial del reductor de engranajes, sino también el costo total de propiedad, incluidos los costos de instalación, mantenimiento, reparación y reemplazo durante el ciclo de vida previsto del reductor. A largo plazo, este análisis ayudará a identificar las opciones más rentables.
Validar la selección a través de pruebas de validación Se recomienda realizar pruebas de validación antes de finalizar la selección. Esto incluye probar muestras de los reductores de engranajes seleccionados en condiciones de funcionamiento simuladas para verificar su rendimiento, fiabilidad y durabilidad.
En resumen, el proceso de selección del reductor de engranajes es integral y requiere un enfoque sistemático. Al considerar cuidadosamente los requisitos de la aplicación, calcular los parámetros necesarios y consultar los datos del fabricante y los estándares de la industria, los ingenieros pueden elegir los reductores de engranajes que ofrecen un rendimiento confiable y eficiente para su aplicación específica.
Ahora la oferta